Sign in to follow this
Followers
0
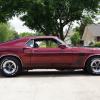
Have Questions on Engine Leak Down Test
By
prayers1, in 1969-70 Technical Forum
By
prayers1, in 1969-70 Technical Forum