Sign in to follow this
Followers
0
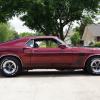
Need HELP-Did the bodyshop mess up!!!
By
prayers1, in 1969-70 Technical Forum
By
prayers1, in 1969-70 Technical Forum