Sign in to follow this
Followers
0
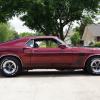
What can you tell me about rolled fenders
By
prayers1, in 1969-70 Technical Forum
By
prayers1, in 1969-70 Technical Forum